by Erin Long | Jan 7, 2025 | Blog Posts, Uncategorized
Welding and grinding are two essential processes in many industrial operations. Both generate dust and fumes that must be safely controlled. A common question in these environments is whether the same filtration system can be used for both processes. It is technically possible to use a single dust collection system. However, there are several critical considerations to address to ensure safety and efficiency. Simply combining welding fumes and grinding dust without proper design could lead to significant risks.
Understanding the Differences Between Welding Fumes and Grinding Dust
Welding and grinding produce very different types of contaminants:
- Welding Fumes: These consist primarily of fine metal oxides generated as a result of the welding process. Welding fume particles are typically very small (sub-micron size). Inhaling them is hazardous as they often contain materials such as iron oxide, manganese, or chromium, depending on the welded metal.
- Grinding Dust: Grinding produces larger particulates and can include a mix of materials. This dust may contain metal shavings, abrasives from grinding wheels, and other byproducts. The composition and size of grinding dust can vary significantly. It depends on the materials being worked on and the tools being used.
Mixing these two types of particulates in the same dust collection system can lead to unintended consequences. For example, combining metal fumes with abrasive grinding dust may alter the dust’s characteristics, potentially making it more combustible or flammable. This risk is amplified because sparks are often present in both processes.
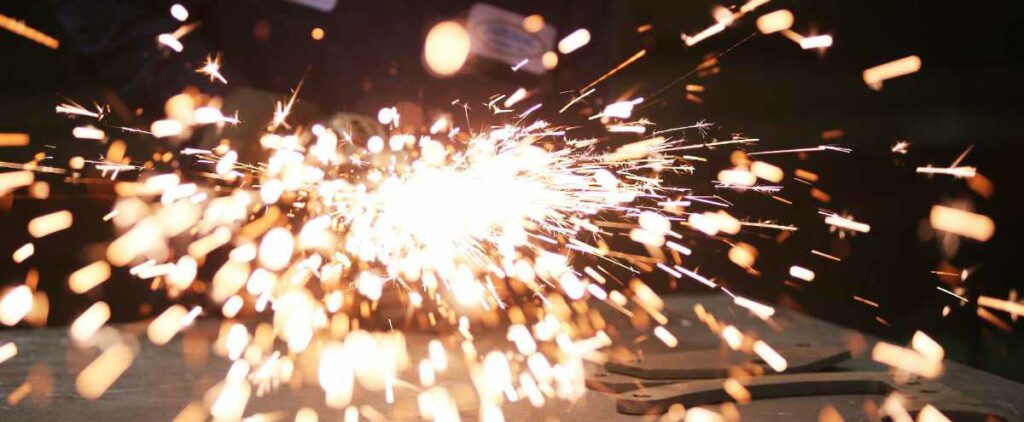
Fire and Explosion Risks in Combined Systems
Sparks are a major fire hazard when combined with combustible dust. Both welding and grinding produce sparks that have the potential to travel through the extraction system and ignite flammable particulates.
If mixing welding and grinding dust, the potential for combustion increases because the dust characteristics are unpredictable. This requires careful design of the dust collection system to include features like spark arrestors and fire suppression systems. Ignoring these precautions could lead to catastrophic fires or explosions in the workplace.
Sizing the Dust Collection System Properly
Another important consideration when using the same system for welding and grinding is the sizing of the dust collector. The efficiency of a dust collection system depends heavily on the air-to-cloth ratio—the volume of air passing through a square foot of filter media.
Welding fumes, being fine and lightweight, allow for a higher air-to-cloth ratio. In contrast, grinding dust, which includes larger and heavier particles, requires a lower air-to-cloth ratio to ensure proper filtration. If using the same system for both processes, it’s critical to size it conservatively to accommodate the demands of grinding dust. A system designed solely for welding fumes may not effectively handle grinding dust. This leads to reduced efficiency, increased filter wear, and higher maintenance costs.
To safely extract both welding and grinding contaminants, the dust collector should have a low enough air-to-cloth ratio to handle the larger grinding particulates without compromising on the capture of fine welding fumes.
Designing a Safe, Effective Solution for Welding and Grinding Dust and Fumes
While using a single dust collection system for both welding and grinding is feasible, it must be carefully designed to address the specific challenges of each process:
- Dust Hazard Analysis: Conduct a thorough analysis to understand the composition, combustibility, and volume of the dust and fumes produced.
- Proper Filtration: Select filter media that can suitably handle both fine welding fumes and larger grinding particulates.
- Spark Control: Incorporate spark arrestors, fire suppression systems, and explosion vents to mitigate fire hazards.
- Sizing and Airflow: Design the system with an appropriately low air-to-cloth ratio to accommodate grinding dust while still effectively filtering welding fumes.
- Segregation (Optional): In high-risk environments, consider separate extraction systems for welding and grinding to minimize safety concerns.
While welding and grinding can share the same dust and fume extraction system, it is not always the recommended solution. Mixing welding fumes with grinding dust poses risks related to combustibility, fire hazards, and filtration efficiency. If you choose to use a common system, it’s essential to design it with care—accounting for the specific needs of both processes, ensuring proper sizing, and implementing safety features like spark control systems.
Ultimately, a well-designed dust collection system will not only keep your facility safe and compliant but also improve air quality, protect equipment, and enhance overall productivity. If you are unsure whether a shared system is appropriate for your operation, consulting with dust collection experts can help you make the best decision for your facility’s needs.
Read more
by Erin Long | Aug 30, 2019 | Uncategorized, Woodworking
Choosing the right type of dust collector for your industrial woodworking application can improve safety and save money. Wood dust is highly combustible, and as a result, it causes many accidental fires and explosions. Industrial woodworking applications may include cutting, planing, sanding, routing, and sawing. The process and the type of wood help determine your dust collector options.
Wood Dust Filtration Challenges
Many industrial woodworking facilities use several different machines for wood processing. As a result, they produce dust that contains a variety of particle sizes and characteristics. This makes each woodworking dust collection system a unique project.
Because wood dust can absorb water, in a moist environment it can become sticky and start to form clumps of material. Also, wood particles can be sharp-edged and abrasive. The most serious challenge, however, is the highly combustible nature of wood dust. Regardless of the type of dust collection system, it must always include appropriate fire and explosion safety devices.
What Are Your Choices?
Wood dust collection may use any type of dust control system. This includes cyclones, baghouses, and cartridge collectors. Often, a woodworking application may use more than one type of dust collector.
For example, a company that produces large pieces of wood and fine sawdust may use a cyclone to drop out the large material. Then the airflow may proceed to a cartridge collector for the capture of the fine dust. Another company may use a baghouse for wood dust because the material is sticky or fibrous.
The Cyclone
First option: a cyclone, which removes large pieces of wood or clumps of sticky material. Because a cyclone doesn’t use any filters, it can handle abrasive or other harsh materials. A cyclone only handles material heavy enough to fall out of the air stream. Lighter dust will pass through.
As part of a wood dust collection system, a cyclone works to remove the rougher materials that might cause problems in a baghouse or cartridge collector. With finer dust, however, you need a dust collector that captures small particles. This means using filters.
The Baghouse
One option for a dust collector with filters is baghouse. Baghouses use long cloth bags as filters. These collect dust on the surface. To keep them working efficiently, the baghouse cleans its bags by using fans or compressed air. Older baghouses may shake the bags to clean them, but this is a messy and high maintenance method.
Baghouses excel at capturing fibrous or sticky dust. They can handle very heavy dust loading, and they also handle high temperatures. One serious downside of a baghouse is the work required to change the bags. One baghouse may have hundreds of bags, and nobody wants the job of replacing all of them in a tight, dirty space.
Size can be another issue with baghouses. To provide the needed surface area, baghouses need lots of bags, making them very large. Not all facilities may have any issue with this, but some may seek a smaller, more compact option.
The Cartridge Collector
That smaller option is a cartridge dust collector. The pleated cartridges provide much more surface area in a smaller space. The woodworking industry uses cartridge collectors more often as they prove their usefulness. Woodworking applications such as sanding dry wood produce very fine sawdust.
A cartridge dust collector efficiently captures this fine dust. Pulses of compressed air clean the filters. This gives them a longer filter life, especially in vertical cartridge collectors. Cartridge collectors work well for fine sawdust, but they also work well for dust that contains contaminants that need to be captured.
Some contaminants in wood dust may include resins, adhesives, and dye pigments. Since any of these could cause illness or harm if released into the air, a dust collection system must control these materials. A cartridge collector has the highest filter efficiency for small particles. This means that it captures even very fine dust. With added after-filters, the efficiency goes even higher. Spunbond filter material with PTFE coating will resist most materials, even sticky or damp dust.
What to Consider Before Choosing a Dust Collector for Woodworking
These factors will affect what type of dust collection system you may need. However, this is not a substitute for having your facility assessed by a dust collection professional. Factors include:
- Particle size
- Abrasiveness of dust
- Type of woodworking process
- The moisture content of the material
- Contaminants
- Space and cost considerations
- High-temperature conditions
- Amount of dust loading required
- Filter and maintenance costs
For example, a baghouse will require more downtime and maintenance labor to change out filter bags. Cartridge collector filters take less time and effort to replace. On the other hand, bags withstand high temperatures and harsher materials.
Industrial Woodworking Dust Control
Whatever type of dust collection system you choose for your wood dust, make sure the system meets NFPA standards for fire and explosion safety.
Wood dust fires are very common and can spread very quickly. A well-designed system will have safety features to protect people and property. All types of woodworking dust collection require these controls.
Wood dust can easily escape and accumulate around work areas. You can control this fire hazard by using source capture dust collection, where the system captures dust at the source. For example, hoods located over woodworking machines can pull the dust away before it gets loose in the facility.
The best way to find out which type of dust collector is right for your application is to contact one of our dust collection experts. We can discuss your woodworking processes and help you choose the type of system that will work best to control your wood dust.
Read more
by Erin Long | Apr 17, 2019 | Weld Fume
Any of our competitors will sell you a weld fume collector, but how many of our competitors are welders themselves? We are proud to be a welding fume collection company. If you go out into our shop, you’ll see our CMAXX dust and fume collector right in the middle. It’s protecting a shop full of welders who are working on new dust and fume collectors.
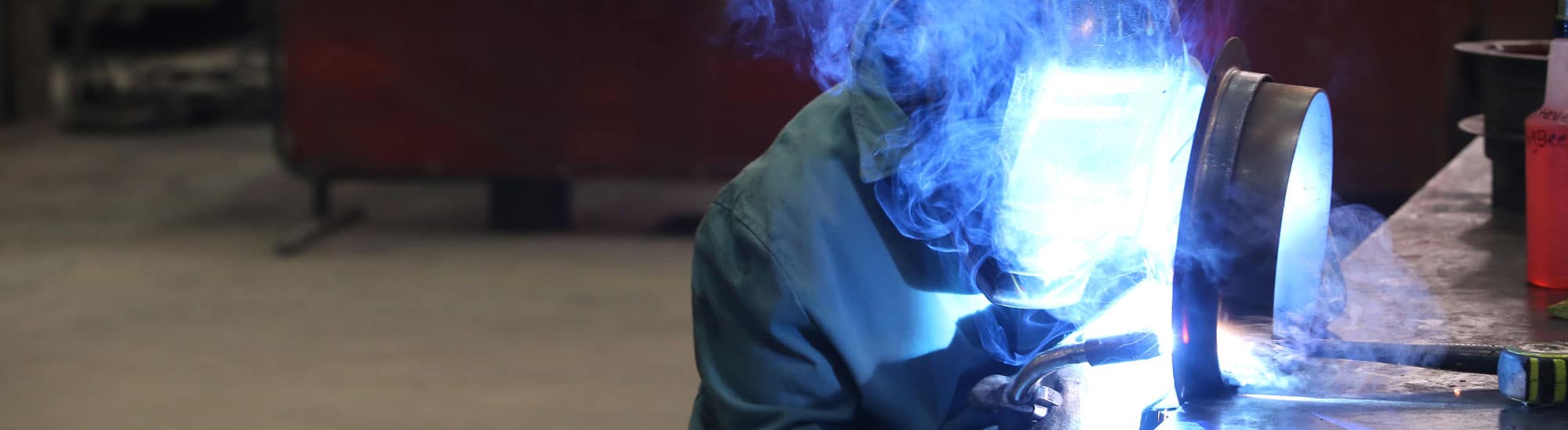
Fume Collectors Welded, Not Bolted
While most of our competitors bolt the pieces of their dust and fume collectors together, Imperial Systems’ collectors are welded solid with no external bolt holes. Because our collectors are welded and not bolted, we understand welders’ fume collection needs. We know our weld fume collector works in the field because it works in our shop.
Our own welders test our fume collection system every day. The safety of our own employees drives us. As a welding fume collection company, our systems can’t just be good enough to sell to you. They must be good enough to put in our own shop.
Because our competitors do so much bolting and not so much welding, their systems don’t get put through the same test that ours do. If our fume collection system didn’t work for welders, our welders wouldn’t be happy with it.
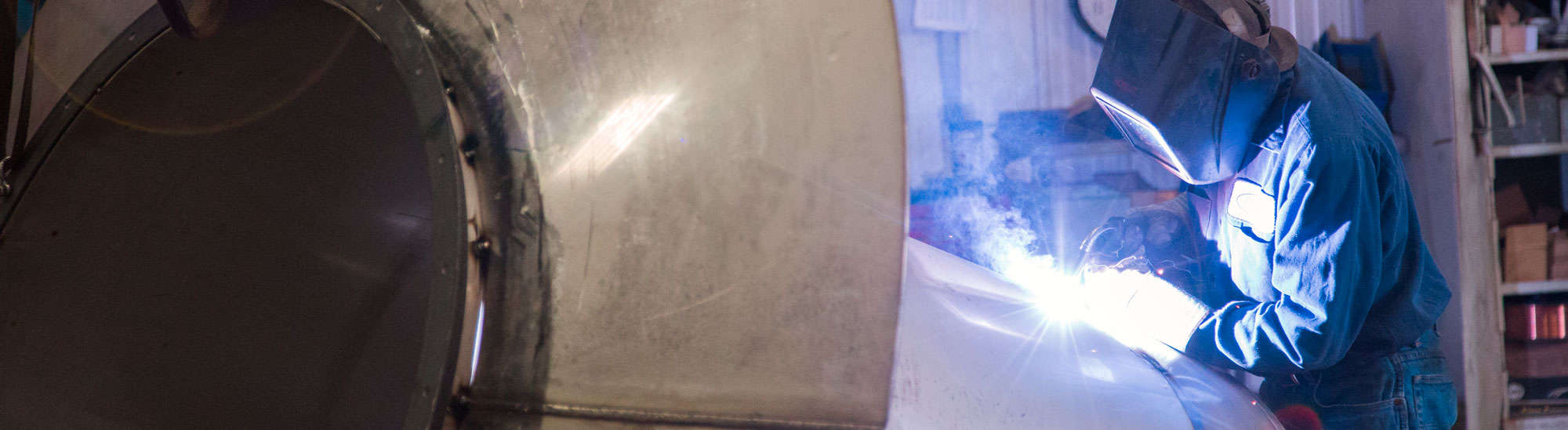
By Welders, For Welders
The person who cares most about how a machine works is the person who uses it every day. For welders doing their jobs every day, a fume collection system needs to work. They care about their work environment and whether it’s clean and pleasant to work in. They care about their health and what they’re breathing.
As a welding fume collection company, it’s our responsibility to make products that welders like and trust. We always encourage and value feedback from our welders about ways our weld fume collectors could be improved. We know that if our own welders in our shop aren’t satisfied with the way our CMAXX works, people who purchase it for their own shops won’t be satisfied either.
Our welders are proud of the quality of their work. As a weld fume collection company we take pride in giving our welders the safest, most pleasant environment to work in. Our goal must always be the highest air quality possible.
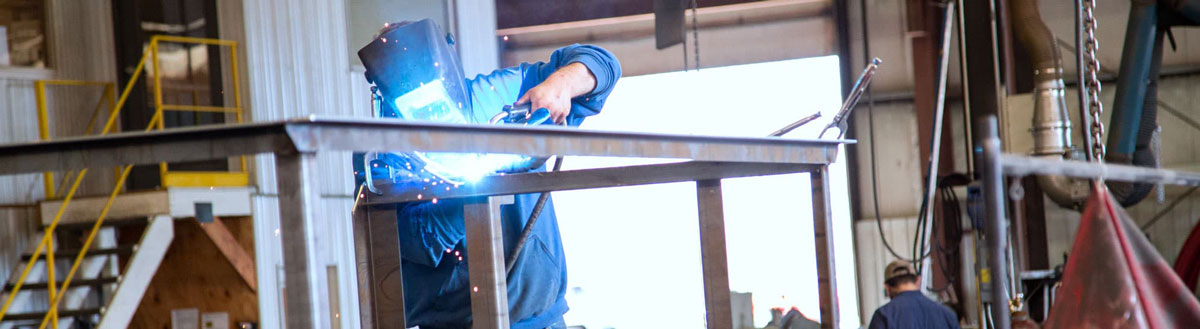
What’s Wrong with Bolts
Why do we weld our fume collectors instead of bolting them together like the competitors? Bolting the panels together probably saves some time over the work of a skilled welder. When you’re choosing a weld fume collection company, however, quality beats cutting corners. Bolts can come loose, and bolt holes rust and allow water inside the collector.
As a solid welded piece with no external bolt holes, the CMAXX has no bolt holes to rust. The quality work of our welders produces the most durable, weather-resistant fume collector on the market. It allows us to offer the longest warranty in the industry.
Our competitors choose bolts over welding, probably because that’s how they’ve always done it. Some competitors, though, have started to copy our design, including the solid welding instead of bolts. Don’t fall for these CMAXX wanna-be products. The copycats will never be as good as the original. Many of these copycats aren’t even made in the USA and they don’t go through our most important test: the satisfaction and happiness of our own welders.
With NFPA standards on combustible dust, more and more dust and fume collectors are being located outside. This makes it easier and safer to vent an explosion, but it exposes the collector to the elements. After many years of rain and snow, bolt holes will show corrosion and rust. Unlike bolt holes, our welds don’t leave the metal weak to rusting.
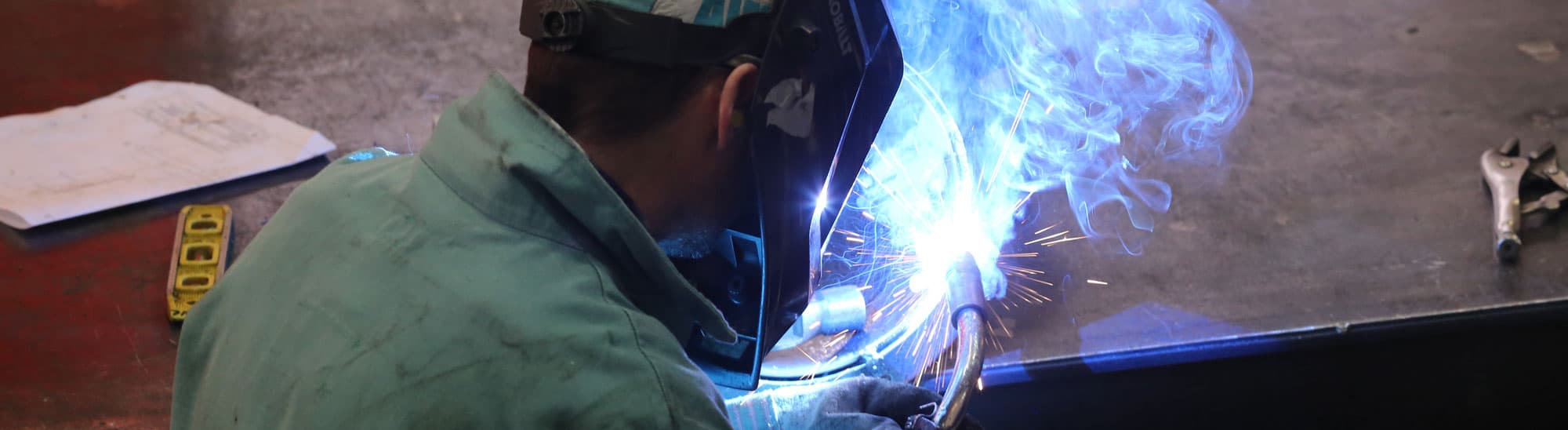
Why We Do What We Do
We are a welding fume collection company because welders deserve to be safe and healthy at work. All welders, including those in our own shop, deserve the basic right to clean air in the workplace. Our welders test our weld fume collectors while they’re making them. Our shop relies on our systems to do a good job. If our own welders trust the product they build, that means you can trust it in your shop too. The CMAXX is a product built by welders, for welders, from our weld shop to yours.

Read more
by Erin Long | Feb 7, 2019 | Weld Fume
Welding can be a dangerous job. Specifically, weld fumes contain a mixture of metals that can cause serious health damage. However, welders can work safely and stay healthy with an industrial ventilation system keeping the air clean.
What Are Some Health Risks for Welders?
Welders work very closely to the metal they are welding. So this puts them in the path of the weld fumes that rise from the heated metal. Many components of these fumes are dangerous to inhale. But industrial ventilation systems can remove these fumes.
Welders working on iron are at risk of pulmonary siderosis, sometimes known as “welder’s disease.” This is where iron particles build up in the lungs and damage them. This disease is incurable. Welding causes another disease known as “metal fume fever”. In this case, the lungs react to inhaling metals like nickel or other metals, causing a flu-like illness. Also, cadmium and hexavalent chromium are proven to cause cancer. Further, beryllium is often alloyed with other metals and causes fatal lung disease. Meanwhile, using manganese in welding rods or alloys causes a disease looking like Parkinson’s.
With all these health dangers, ventilation solutions are necessary for welders’ health. Fortunately, an industrial ventilation system will remove weld fumes and let welders work safely.
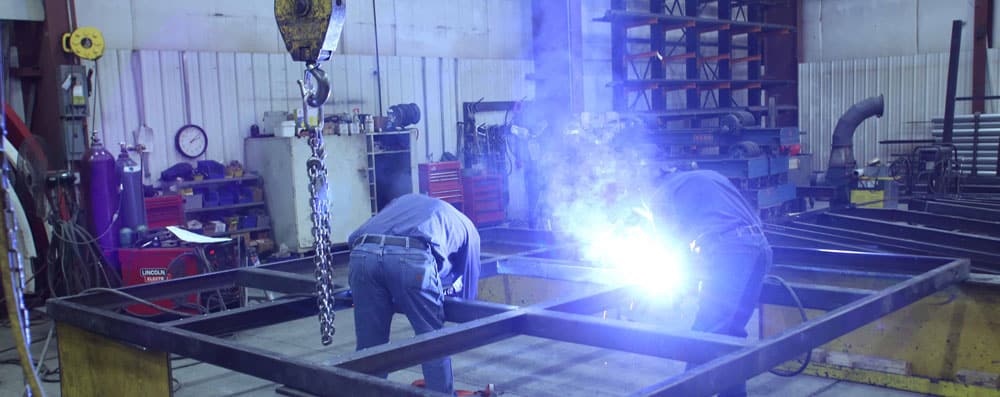
How Should a Plant Ventilation System be Designed?
An industrial ventilation system for welding can be either an ambient or source capture system. Both provide ventilation solutions, but in different ways.
An ambient system circulates all the air in the facility through a dust collector. Then it returns clean air. This removes weld fumes from the whole space.
A source capture system has ventilation points at the areas where the welders work. Examples of these points can be fume arms, hoods, or downdraft tables. The air pulls the fumes directly away from the welder’s breathing area. The plant ventilation system filters the air through a dust collector.
You can use both kinds of systems for industrial ventilation. Source capture works well when the dust comes from individual machines or work areas that don’t move around. Install a hood or arm to handle ventilation from those sources.
Applications can include fume extraction from robotic weld cells or welding stations. In other instances, they can include bin vents, blenders, and conveyors. Source capture can usually manage any process that generates dust.
Connect a hood, fume arm, or downdraft table to the general air ventilation system. Design the system with many “drops,” or source capture points. This requires a skillful system designer to balance the airflow. A badly designed system may not have consistent ventilation in all areas of the plant.
An ambient system works well for cleaning all the air in the facility. An industrial ventilation system like this might be used when people are creating fumes by welding in different areas or moving around. If source capture points can’t catch everything, an ambient strategy may be needed. This will ensure the plant ventilation system is sufficient.
Industrial Ventilation Systems for Welder Health
With so many ventilation solutions possible, you can protect welders in every type of facility from weld fume health hazards. Have your system designed by a trained pro will make sure every area of the facility has clean air.
If a hazard can’t be removed completely, OSHA and other safety groups like ACGIH recommend engineering controls. A plant ventilation system is a form of engineering control. Welders need to work around weld fumes. The best way to minimize the risk is to remove the fumes before they can cause harm.
Make sure welders in your facility stay healthy. Contact us about an industrial ventilation system designed for your needs.
Read more
by Erin Long | Jan 23, 2019 | Weld Fume
This weld fume extraction guide takes a look at the many ways to collect and remove weld fume from a facility. When not properly taken out of the work area, weld fume can cause some serious health issues for welders.
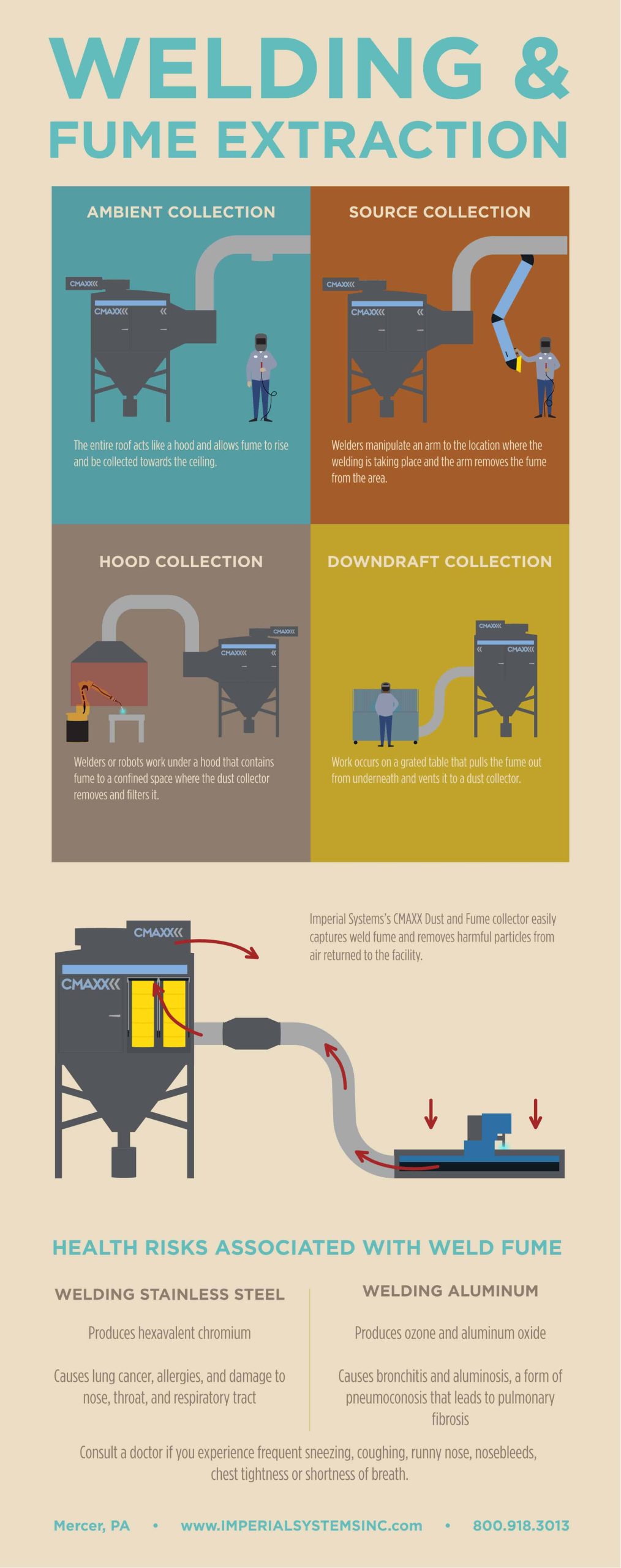
Weld Fume Extraction Methods
- Ambient Collection – The entire roof acts like a hood and allows fume to rise and be collected towards the ceiling. Ductwork runs with inlets above the work area to clear the fumes.
- Source Collection – Welders manipulate an arm to the location where the welding is taking place and the arm removes the fume from the area.
- Hood Collection – Welders or robots work under a hood that contains fume to a confined space where the dust collector removes and filters it.
- Downdraft Collection – Work occurs on a grated table that pulls the fume out from underneath and vents it to a dust collector.
Health Risks Associated with Weld Fume
Welding Stainless steel
- Produces hexavalent chromium, a dangerous valence state of the element chromium. Chromium metal is added to alloy steel to increase hardenability and corrosion resistance.
- Causes lung cancer, allergies, and damage to the nose, throat, and respiratory tract
Welding Aluminum
- Produces ozone and aluminum oxide. TIG, MIG, and plasma-arc welding typically produce ozone, a highly toxic gas. Aluminum oxide forms from the base and filler materials and exists in the welding fumes.
- Causes bronchitis and aluminosis (aluminum lung), a form of pneumoconiosis that leads to pulmonary fibrosis
Consult a doctor if you experience frequent sneezing, coughing, runny nose, nosebleeds, chest tightness, or shortness of breath.
Weld Fume Extraction Equipment and Experts
The CMAXX Dust & Fume Collector by Imperial Systems is the best choice for removing weld fume from your facility and keeping your employees safe. Our sales and product engineers will design and dust and weld fume collector specifically for your application. Contact us today.
Read more
by Scott Stearns | Jan 9, 2019 | Grain

The grain and animal feed manufacturing process has always been an area of concern when it comes to combustible dust. Therefore, the NFPA has a standard specifically for this industry: NFPA 61 (Standard for the Prevention of Fires and Dust Explosions in Agricultural and Food Processing Facilities).
OSHA also highly regulates dust hazards in the animal feed processing industry. In fact, OSHA has leveled some fines higher than $1 million for recent fatal explosions in this industry.
Explosions at grain and feed mill processing plants kill several people every year and cause many explosions. Certainly, the feed manufacturer is especially prone to these accidents because their materials are often in dust form and just need an ignition source to explode.
The best way to control dust at a feed processing plant (and the way recommended by NFPA and OSHA) is with a dust collection system. However, handling all the dust in your facility is going to require a major investment… so, how do you make sure you get the best system for your money?
The key to a safe, efficient system is having it designed by a company with experience in your industry and a track record of not cutting corners. Further, a cheap system will cost you money in maintenance and attempts to fix design flaws.
ELEMENTS OF A GOOD SYSTEM DESIGN FOR FEED MANUFACTURING:
- Proper airflow through the entire system
- Correctly sized fans
- Explosion and fire protection
- Good dust containment
- Correctly sized dust collector
- Enough filter area
Let’s look at each of these to see why they’re important for you.
PROPER AIRFLOW
If air can’t move through the ductwork efficiently, then there will be places where it slows down or runs into obstructions. As a result, this causes three problems. First, it decreases your system’s efficiency and wastes fan power. Second, it slows down the air so dust can fall out and build up in the duct. Third, dust traveling through a badly designed system can cause wear and tear on the duct at bends and corners.
CORRECTLY SIZED FANS
If the fan isn’t big enough for the job, it won’t keep dust flowing through the system. Also, if air moves too slowly it won’t pick up dust at the capture points and it won’t keep it moving through the ducts. Consequently, dust built up in ductwork can cause fires.
EXPLOSION AND FIRE PROTECTION
Any dust collection system for feed manufacturing has to have proper fire protection. Some examples of this include spark traps, abort gates, explosion isolation valves, or extinguisher systems. Unfortunately, there’s no one-size-fits-all solution. An experienced system designer will help you choose the best tools to protect your facility and your employees.
GOOD DUST CONTAINMENT
It doesn’t do much good to have a dust collection system if it isn’t controlling your dust problem. Dust is probably being generated at lots of places in your animal feed processing plant. If the dust collection system isn’t capturing the dust at those spots, it will get loose. In short, nobody wants the facility to be a dusty mess, and it’s also a fire hazard.
CORRECTLY SIZED DUST COLLECTOR
It might be tempting to go for the smallest dust collector that will work for your cattle feed processing plant. Ironically, this might not save you as much money in the long run as you think. This is because an undersized system is going to require more filter changes and other maintenance. Further, if your production expands, that barely-big-enough system may not be able to keep up anymore.
ENOUGH FILTER AREA
A dust collector can’t do its job if its filters can’t function. Every type of system has an ideal air-to-cloth ratio, the amount of filter area that should be available for the air flowing through them. So if you don’t have enough filter area, your filters may get overloaded with dust and stop working. Therefore, they will need replacing more often, which costs money and time.
A dust collection system for feed manufacturing must be designed for this special application. Grain and feed manufacturing facilities like a feed hammer mill can have fine and coarse dust at different parts of the feed mill process. Most feed processing methods have many places where dust is being generated. Also, dust in this application is usually very combustible.
In conclusion, talk to an expert in dust collection system design to keep your facility and your employees safe. Our Imperial Systems professionals will make sure you get the best system for your money without cutting any corners or leaving gaps in your protection.
Read more about safety in hammer mill material handling.
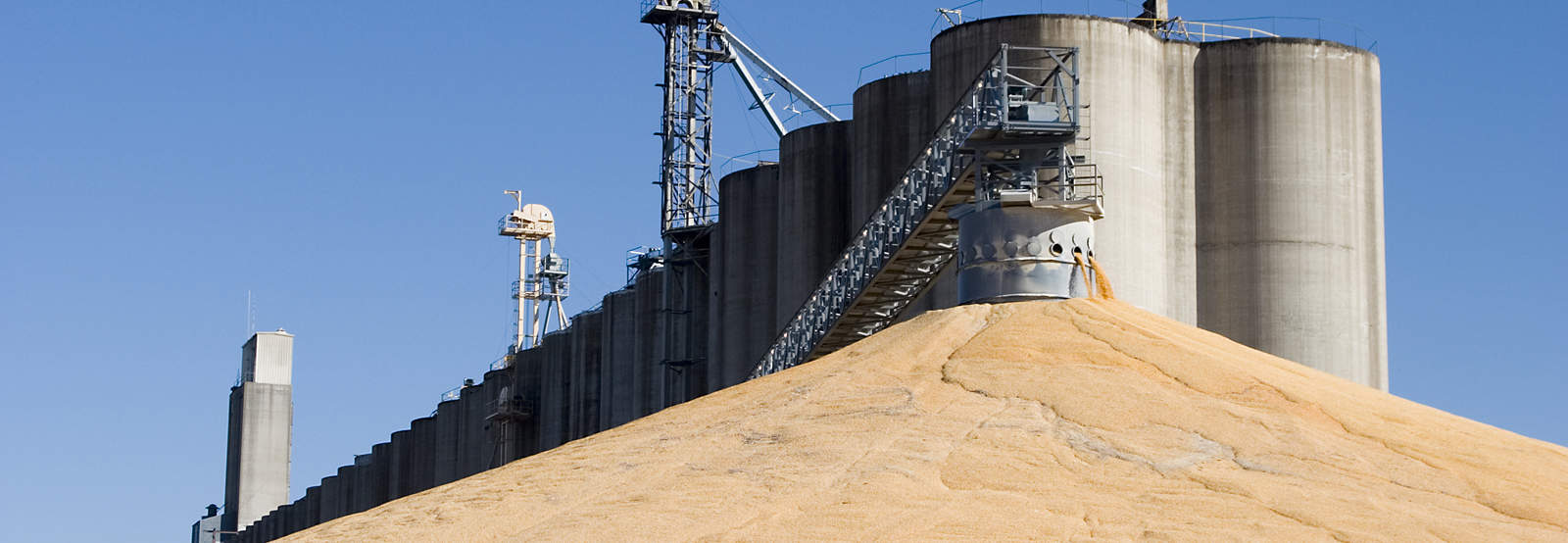
Read more