by Erin Long | Jun 5, 2019 | Uncategorized
For a baghouse to function correctly, system designers need to perform a bag filter calculation. So how do you calculate the air-to-cloth ratio of your bag filters? Some websites offer simple formulas to estimate the correct air-to-cloth ratio. However, a good system designer knows that every application and every material is a little different.
System designers also do a compressed air requirement calculation for bag filters. Because without proper cleaning, bags become covered with dust which throws off the calculated air-to-cloth ratio. Therefore, getting these two calculations right makes sure your baghouse runs at full efficiency.
How to Calculate Air-to-Cloth Ratio in Bag Filters
An air-to-cloth ratio compares the amount of air going through a square foot of filter area. If you know the total CFM of the system and you know the amount of filter area you have, you can calculate this ratio.
For example, if you have 10,000 CFM through your collector and 5,000 square feet of filter area, your ratio is 10,000:5,000. But it’s much simpler to convert this to a ratio of 2:1. The air-to-cloth ratio can be anything from 1:1 to 3.5:1.
What makes the difference in bag filter calculation? Often, it’s the type of dust that the system collects. Different types of material will change how you calculate the air-to-cloth ratio in filter bags. Most companies that design baghouses know the general cloth area of their filter bags. A filter bag calculation can also be made because filter bags are round. If you know the diameter of the bag, multiply this diameter by 3.14 to get the circumference. (Think back to high school math and the circumference of a circle.)
Therefore, the circumference of the bags (diameter of the bag x 3.14) multiplied by the length of the bag will give you an approximate bag surface area. There are 144 square inches in a square foot. Since the diameter of the bag will be measured in inches, the bag surface area must be measured in inches too. Use this surface area in the air-to-cloth ratio.
Ask the Manufacturer First
You may never need to know how to do these calculations. Fortunately, many filter bag manufacturers know the general surface area of their bags. Also, a system designer usually knows the surface area of bags that need to go in a collector. What you do need to know is why the surface to air ratio matters. Consequently, a wrong bag filter design calculation can result in a collector with a ratio that causes serious problems.
Importance of Correct Air-to-Cloth Ratio Calculations
The correct air-to-cloth ratio determines the efficiency and life span of your filters. Above all, buying and replacing filters may be the most expensive and time-consuming part of dust collector maintenance. The correct bag filter calculation extends the life span of your filters and keeps them working efficiently. Not having enough cloth for the air in your system results in low filter life and damaged or overloaded filters.
Different materials will require different air-to-cloth ratios. Similarly, different applications also demand changes to the air-to-cloth ratio. An ambient system usually filters the air with a low overall amount of particulate. In contrast, a source capture on plasma cutting collects much more material. Wood, fiberglass, and other materials affect filters differently. Therefore, you should consult with someone who has experience in air-to-cloth ratio calculations for your type of material.
Compressed Air Requirement Calculation for Bag Filters
Even if a system has the correct air-to-cloth ratio, it still needs to clean the filters correctly. For instance, some baghouses are cleaned with airflow from a fan. The fan sizing will be part of the overall system design. Other baghouses use pulses of compressed air to clean the filters. For these, the calculation of compressed air requirements is important.
Compressed air requirement for bag filters determines how long the bags will last and how efficient they will be. Some compressed air cleaning systems are timer operated. This means that pulses of compressed air clean the bag filters at a designed time. Dust collectors can also have differential pressure pulse control. In this case, a rise in the differential pressure triggers a sensor to activate a pulse. The compressed air only pulses when the filters need it. This means that the compressed air requirement for the baghouse is lower.
The size of the piping and valves used can also affect the compressed air. A baghouse should be operated with the bag filters, valves, and other equipment that came with the system, or an appropriate replacement from the manufacturer.
Valves and other parts of the compressed air system can develop leaks and waste compressed air. As a result, there will be less efficient pulsing. Therefore, systems should be checked regularly for any leaks or failing valves. The compressed air requirement calculation for bag filters is only accurate if the entire system operates as designed.
Read more about bag filters here.
Read more
by Erin Long | Jun 5, 2019 | Case Studies
A sawmill company with facilities in Pennsylvania and New York had a challenging dust problem. Fine sawdust from their band mills was filling the air. The constant production of dust created an unpleasant work environment for employees. As a result, the facility needed a form of sawdust collection.
Ryan is responsible for creating a better, healthier environment for sawmill employees. But he wasn’t going to rush in with a hasty solution. He was going to take the time to do it right. So he would work with equipment suppliers to design the system his company needed.
In the process of designing a dust collection system, Ryan worked with Hermance Machine Company. Through them, he learned about Imperial Systems, Inc and their BRF baghouses. In addition to the BRF, he also looked at the products made by several competitors to compare them.
Ryan paid a visit to Imperial Systems. He got a chance to look at the BRF baghouse and the manufacturing process. “I saw a good product,” he says. He also liked the idea of working with a local company.
Ryan had been working on the air filtration project for several years. He planned out the ductwork, fans, and other details of the system. A significant part of the investment would be the baghouses. So it was important to choose the right company to build them.
Sawdust Collection Solution
Imperial Systems provided Ryan’s company with two reverse-air 14-foot BRF baghouses as well as airlocks, one for each of the two locations.
“Having this system has completely changed the environment of the sawmill,” Ryan says. “It’s gone from being a poor environment for employees to having crystal clear air.”
Ryan has succeeded in his goal of making the sawmills a better, healthier place to work for everyone. He says that the BRF baghouses are working exactly as he expected them to. He’s certainly satisfied with the help and service Imperial Systems has provided. This includes working with him through some glitches to make sure everything works the way he needs it to.
At Imperial Systems we take pride in working with our customers throughout the process, and our service doesn’t stop when the equipment install is complete. We’re there to work with you, iron out any bugs, and help you meet your air quality and safety goals. Sawdust collection is only one of many applications for which we have solutions. So contact us today about your challenging dust or fume problem.
Learn more about woodworking dust collection.
Read more
by Erin Long | Jun 4, 2019 | Abrasive Blasting
The Problem
Abrasive blast equipment operation continued to be a problem for a pipe manufacturer in Arkansas. The company produces pipe for water, gas, oil, and other industrial markets. They use abrasive blast cabinets in their production to clean the metal surfaces. Round steel shot is the abrasive blast media. However, this fugitive material accumulated in the facility. Their existing dust collector was also pulling it up into the ductwork. As a result, the weight strained the duct.
Further, the company required a system to handle multiple capture points on equipment like bucket elevators and hoppers. They needed to replace the existing dust collector. Initially, they received quotes from other companies who told them they needed a 9,000 CFM system. Unconvinced, the company chose to contact more experienced dust collection experts. They asked the specialists at Air Solutions to come in and review the situation. They wanted to eliminate their problems with a properly designed abrasive blast dust collector system.
The Solution
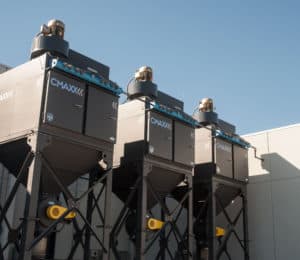
Air Solutions conducted a survey and decided that the system must be rated for 11,000 CFM. It also needed to have air bleed-in ports to keep the system from picking up the steel shot. This arrangement would allow the adjustment of airflow. The control measure ensures that the system picks up dust and other material but not the abrasive blast media.
The survey also determined that existing dust collection on capture points like bucket elevators and feed hoppers was inadequate. So the new system provided dust collection at these points as well as on all the abrasive blast cabinets.
Air Solutions installed a CMAXX dust and fume collection system. They designed an 11,000 CFM system to provide plenty of airflow to all the points of capture. Also, they incorporated air-bleed ports. Enabling adjustability of the airflow, these prevent the system from picking up heavier shot blast media.
Abrasive Blast Equipment No Longer a Concern
The new system certainly creates proper airflow to all capture points on the system. The company uses the bleed-in ports to adjust the amount of ambient air being pulled in. Airflow is now adjustable, helping to make sure they capture dust, not shot blast media.
Increasing the airflow from the proposed 9,000 CFM to 11,000 CFM was key. It makes sure the system is able to handle all the capture points. In addition, the bleed-in ports provide the option to control airflow at various points. The result is complete control over the system and a safer work environment.
Learn more about abrasive and shot blast dust collection.
Read more
by Erin Long | May 30, 2019 | Uncategorized
Manganese is a common metal, and the human body needs it in very small amounts to stay healthy. However, excessive manganese exposure causes serious neurological problems. This is most likely to happen to welders and other metalworkers. You can find manganese as an alloy in steel and sometimes aluminum. Consequently, welding or cutting these metals can release dangerous amounts of manganese.
Limits are already low on health hazards like beryllium and respirable crystalline silica. Manganese is likely to be one of the next materials to see increased regulation. It’s not the only welding exposure that workers need to be concerned about. But it’s another good reason to manage weld fume exposure.
Where would I find manganese in metalworking?
Modern steel production relies on manganese to remove oxygen and sulfur compounds. Many types of steel include it because as an alloy, it makes steel stronger. This means that welding or cutting fumes from steel are likely to contain manganese. In addition, welding manganese exposure can come from manganese contained in welding rods.
Manganese is also used as an alloy with aluminum, where it protects from corrosion. This is not a major source of exposure for metalworkers in general, though. This type of aluminum alloy is popular for food and beverage containers.
What are the limits on manganese exposure?
OSHA’s limit on manganese exposure is 5mg/m3 over an eight-hour workday. NIOSH, the research branch of OSHA, has looked at recent studies. As a result, they recommended a limit of no more than 1mg/m3 over the same period of time.
One research study in 2016 found that over many years of working as a welder, manganese could cause serious neurological symptoms. This is true for exposure levels as low as mg/m3 . The study also found that higher levels of welding exposure to manganese caused more symptoms.
This research shows that just following OSHA regulations may not be enough to prevent manganese exposure symptoms from metalworking.
What are some manganese exposure symptoms?
Manganism is the most severe symptom. This condition of manganese exposure looks like Parkinson’s disease. Specifically, one experiences tremors, balance problems, weakness, and problems with muscle control. Following current OSHA standards, exposure should not be high enough to cause this condition.
However, many researchers find that even at exposure levels much lower than OSHA standards, welders still develop symptoms. Said researchers include the Washington University School of Medicine. These manganese exposure symptoms include muscle stiffness in arms and legs and problems with balance and coordination.
Symptoms take time to appear and usually happen after years of exposure. Although, one could attribute them to just getting old. For this reason, research is needed to show that manganese exposure could cause them.
NIOSH reviewed research on occupational health hazards, leading to a recommendation of lowering the exposure limit. Their findings indicate that welders develop these symptoms faster and more severely than non-welders. Most importantly, even at levels much lower than OSHA standards.
How do you control metalworker exposure to manganese? 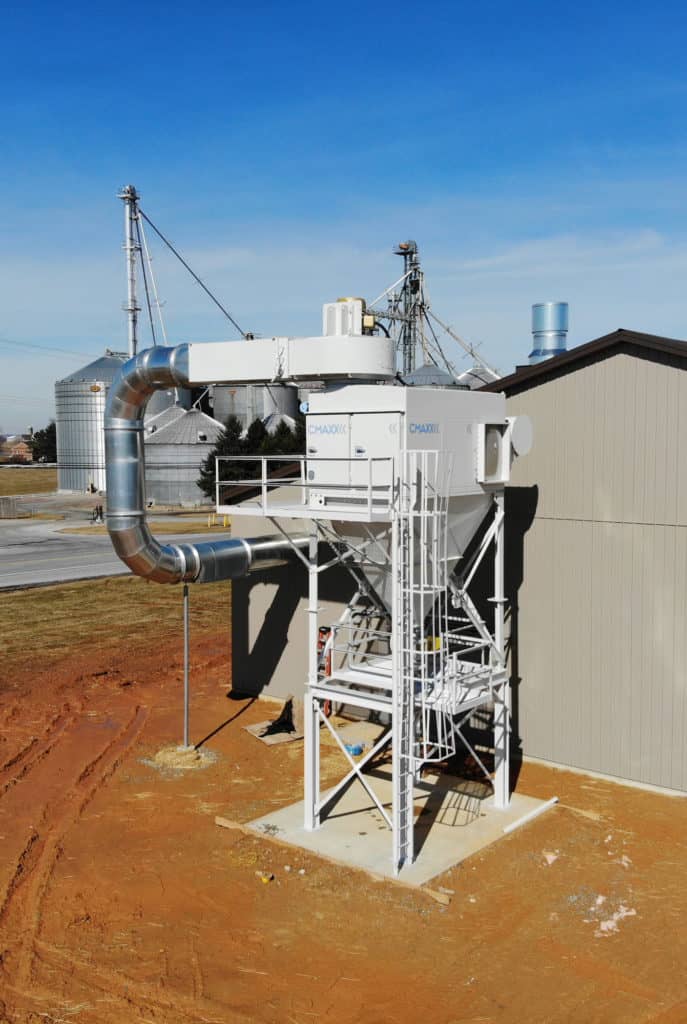
Fumes from welding and cutting metal are hazardous to breathe. Manganese exposure is just one concern. However, because it can cause neurological damage at very low levels, it’s an important issue.
Manage exposure to weld fumes with a well-designed dust and fume collection system. One solution is to use hoods, fume arms, or downdraft tables. These are all types of source capture, and they clear the air around the welder’s breathing space.
Many laser or plasma cutting tables are also downdraft tables and pull fumes down and into the dust and fume collection system.
Fumes can escape from welding stations or cutting tables. An ambient system can filter all the air in the workplace to remove these escaped fumes. As a result, the haze of smoke that some facilities have in the work area is eliminated.
To prevent welders and other metalworkers’ exposure to manganese and other hazardous fumes, contact Imperial Systems. You can also visit the product page to learn more about the CMAXX dust and fume collector.
Read more
by Erin Long | May 23, 2019 | Uncategorized
Dust Safety Science Podcast: Changes in the Dust Collection Equipment Landscape with Jeremiah Wann
“In this episode of the DustSafetyScience Podcast, we interview Jeremiah Wann, President of Imperial Systems, Inc., in Mercer, Pennsylvania, about changes in the dust collection equipment landscape.
Imperial Systems, Inc. is a manufacturer of dust collection equipment and related safety systems. In his position as president of the company, Jeremiah has seen a lot of changes in the field over the past couple of decades, so he talks about:
- How the landscape has changed for dust collectors and other dust-related safety equipment
- How awareness has increased among his clients
- The importance of getting your equipment tested as a manufacturer
- Difficult situations where the customer is hesitant about installing combustible dust safety equipment
Jeremiah’s discussion has immense value because he brings a different perspective to the combustible dust safety issue. He is not a consultant, and he doesn’t serve on any NFPA boards. He is representative of a group that includes facility managers, equipment operators, equipment manufacturers, and insurance companies, and has an experience-based understanding that has enabled him to write several blog posts about combustible dust standards and measurement systems.”
Read more