by Erin Long | Mar 5, 2019 | Hidden from Archive
In November, 14 members of the Imperial Systems team and representatives from across the country travelled to Atlanta for FABTECH 2018. As one of the biggest fabrication trade shows in the country, FABTECH is always an opportunity for us to put the CMAXX and other products on display. It’s also a great opportunity to network and meet others in the industry, including potential new representatives and customers.
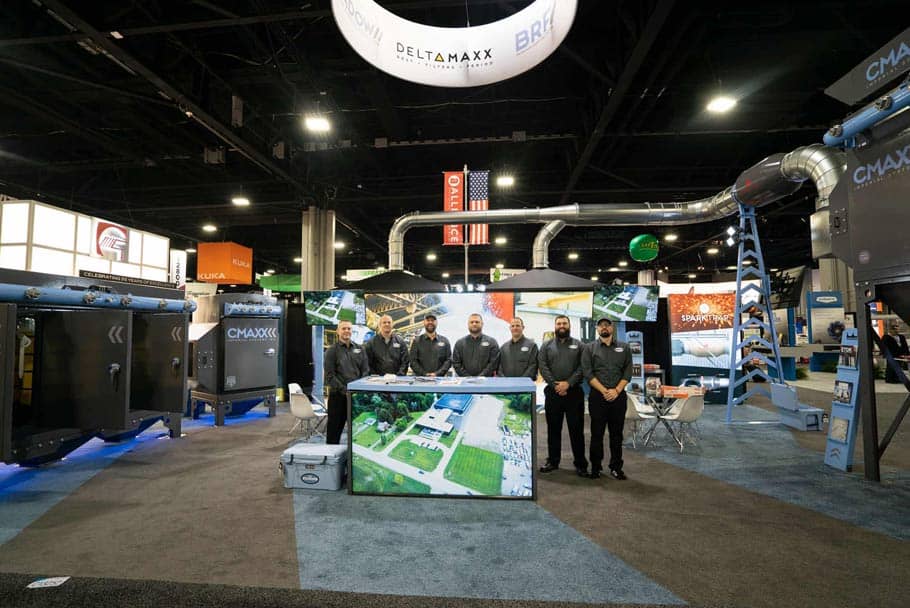
“This year was our best turnout ever,” says Justin Badger, Imperial Systems Sales Manager. Not only did the Imperial Systems booth draw attention with its three CMAXX collectors and other equipment on display, but four other companies also had CMAXX collectors in their own booths. AKS Cutting Systems, Koike, Dynatorch, and Plasma Automation each displayed a CMAXX on their own equipment at the show.
Imperial Systems staff and representatives had the opportunity to meet and talk to many potential customers over three very busy days. The Imperial Systems booth looks better every year as the marketing team works with the sales team to draw attention to our products. This year, an exciting new product was the Rhino Drum, an explosion-tested drum kit recently added to the company lineup.
This was the first year for the Imperial Systems booth to display three CMAXX collectors, and the first time four other manufacturers had their own CMAXX collectors on display with their own equipment. FABTECH is a chance every year for Imperial Systems to demonstrate our growth as a major player in the dust and fume collection market.
“It’s an exhausting couple of days, but it’s completely worth it,” a sales representative says. “It’s amazing how many people come by the booth and want to check out the CMAXX. They want to open the doors, try out the lift rails, check out the filters. They’re always really impressed with the quality.” With more people visiting the booth this year than ever before, more people got to appreciate our products and meet our staff in person.
Read more
by Erin Long | Feb 7, 2019 | Weld Fume
Welding can be a dangerous job. Specifically, weld fumes contain a mixture of metals that can cause serious health damage. However, welders can work safely and stay healthy with an industrial ventilation system keeping the air clean.
What Are Some Health Risks for Welders?
Welders work very closely to the metal they are welding. So this puts them in the path of the weld fumes that rise from the heated metal. Many components of these fumes are dangerous to inhale. But industrial ventilation systems can remove these fumes.
Welders working on iron are at risk of pulmonary siderosis, sometimes known as “welder’s disease.” This is where iron particles build up in the lungs and damage them. This disease is incurable. Welding causes another disease known as “metal fume fever”. In this case, the lungs react to inhaling metals like nickel or other metals, causing a flu-like illness. Also, cadmium and hexavalent chromium are proven to cause cancer. Further, beryllium is often alloyed with other metals and causes fatal lung disease. Meanwhile, using manganese in welding rods or alloys causes a disease looking like Parkinson’s.
With all these health dangers, ventilation solutions are necessary for welders’ health. Fortunately, an industrial ventilation system will remove weld fumes and let welders work safely.
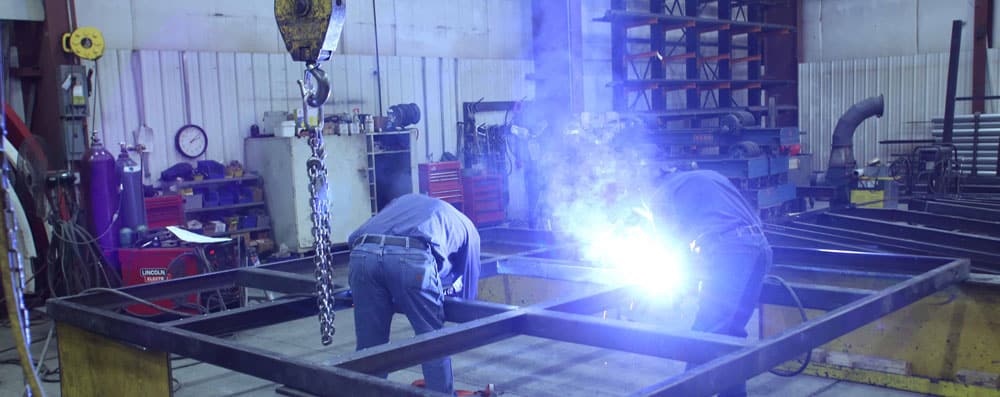
How Should a Plant Ventilation System be Designed?
An industrial ventilation system for welding can be either an ambient or source capture system. Both provide ventilation solutions, but in different ways.
An ambient system circulates all the air in the facility through a dust collector. Then it returns clean air. This removes weld fumes from the whole space.
A source capture system has ventilation points at the areas where the welders work. Examples of these points can be fume arms, hoods, or downdraft tables. The air pulls the fumes directly away from the welder’s breathing area. The plant ventilation system filters the air through a dust collector.
You can use both kinds of systems for industrial ventilation. Source capture works well when the dust comes from individual machines or work areas that don’t move around. Install a hood or arm to handle ventilation from those sources.
Applications can include fume extraction from robotic weld cells or welding stations. In other instances, they can include bin vents, blenders, and conveyors. Source capture can usually manage any process that generates dust.
Connect a hood, fume arm, or downdraft table to the general air ventilation system. Design the system with many “drops,” or source capture points. This requires a skillful system designer to balance the airflow. A badly designed system may not have consistent ventilation in all areas of the plant.
An ambient system works well for cleaning all the air in the facility. An industrial ventilation system like this might be used when people are creating fumes by welding in different areas or moving around. If source capture points can’t catch everything, an ambient strategy may be needed. This will ensure the plant ventilation system is sufficient.
Industrial Ventilation Systems for Welder Health
With so many ventilation solutions possible, you can protect welders in every type of facility from weld fume health hazards. Have your system designed by a trained pro will make sure every area of the facility has clean air.
If a hazard can’t be removed completely, OSHA and other safety groups like ACGIH recommend engineering controls. A plant ventilation system is a form of engineering control. Welders need to work around weld fumes. The best way to minimize the risk is to remove the fumes before they can cause harm.
Make sure welders in your facility stay healthy. Contact us about an industrial ventilation system designed for your needs.
Read more
by Erin Long | Jan 30, 2019 | Uncategorized
The CMAXX is a vertical pulse-jet dust collection system. So how does a dust collector work? What’s going on inside there, and why is it designed the way it is?
The concept is basic: dirty air goes in, dust or particulate gets removed, and clean air comes out. However, the details become important when you’re looking for the right central vacuum system for your machinery.
Considering a shop dust collector system for your business? If so, this information may be helpful for you.
Dust Collection System Design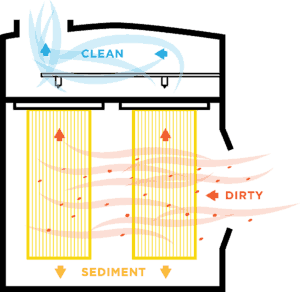
The CMAXX is a reverse pulse-jet cartridge dust collector. The best way to explain what this means is to go on a tour of the path that air follows through the dust collection system.
Dirty Air
- Dirty air containing particles of dust enters the collector through the ductwork. Fans either push or pull the air through the ducts.
- The air hits a set of baffles, which are angled pieces of metal that slow it down. As a result, this keeps the dust from hitting the filters at full speed.
- Then the air enters what we call the dirty air plenum. This just means the side of the collector where the air is dirty. At the bottom of this space, collected dust drops out into a drum or hopper.
Dust Capture
- Next, the air passes through the dust collector’s cartridge filters. In the CMAXX, these hang vertically from the tube sheet, which is the metal sheet separating the dirty and clean air spaces.
- Pleating the filters gives them more surface area. DeltaMAXX filters are also coated with a nanofiber material. This makes the spaces that the air must go through smaller.
- The filters capture the dust. Some of it falls off. Some of it sticks to the filters. Gaskets at the top of each filter seal it to the tube sheet to keep dust from sneaking through.
Filter Cleaning
- A pulse of compressed air blows into the filters. Because the pulse of compressed air goes in the reverse direction of the regular airflow, we call it a reverse pulse-jet collector.
- The pulse of compressed air blows the accumulated dust off the filters. The dust drops out of the collector and the filters are ready to collect more dust.
- On the other side of the filters, filtered air enters the clean air plenum. From there, it can go back into the facility or vented outside.
How Does the Pulse-jet Dust Collection System Clean the Cartridge Filters?
A pulse-jet collector is a very effective type of industrial dust collection system. Diaphragm valves control the compressed air in a pulse-jet collector. Often a timer controls the diaphragm valves. To make the cleaning more efficient, the pulses can also be controlled by differential pressure sensors.
Differential pressure sensors read the air pressure on the dirty air and clean air sides of the filters. The dirtier the filters are, the more resistance they have to air going through them. When the difference in the two pressure readings gets too high, it signals the filter cleaning mechanism.
Using differential pressure sensors makes a pulse-jet dust collector more efficient because it reduces the use of compressed air. It also helps the cartridge filters last longer, because the pulses of compressed air cause wear and tear on them.
Pulse-jet dust collection systems are efficient because of this filter cleaning. With an industrial dust collection system, replacement filters can be a big expense. By making filters last longer, a pulse-jet collector is the most cost-efficient shop dust collection system. Read about offline cartridge filter cleaning.
How Does a Vertical Pulse-jet Dust Collection System Work Better?
Cartridge collectors have the filters in either a horizontal or vertical arrangement. In horizontal dust collection system design, the filters lay on their sides and are stacked on top of each other. The filters hang down from the tube sheet in a vertical filter dust collector.
In a horizontal pulse-jet dust collector, the pulse cleaning causes dust to be blown off the filters. However, because they’re on top of each other, the dust from the top filters falls on top of the others.
In a vertical pulse-jet collector, the dust that pulses off of the filters drops directly down into the hopper. The dust falls free and doesn’t land on the other filters.
Most CMAXX competitors on the market are horizontal dust collectors. Only a few companies make vertical pulse-jet cartridge collectors. Vertical systems are the most effective shop dust collection systems.
In conclusion…
If you’re looking for a central machinery dust collector for your facility, make sure it has a self-cleaning, pulse-jet system. To get a good idea of how the CMAXX works, check our product page. If you still have questions, please feel free to ask us!
Read more
by Erin Long | Jan 28, 2019 | Uncategorized
After you’ve installed your dust collection system, the big initial expense is over. However, you need to plan for your system’s regular maintenance, like replacing the industrial dust collector cartridge filters. Dust collectors that use cartridge filters have become very popular, partly because cartridge filter changes are easier.
Dust collector filters are the part of the system that clean the air traveling through the system. In a pulse jet collector with dust cartridge filters, the filter cleaning system removes dust from the surface of the filters.
All filters, though, will eventually become overloaded with particles and will need to be replaced.
Do they really have to be replaced? Why can’t you just clean them?
Can’t you just take out and clean the dust collector cartridge filters so they’ll work better again?
You can, and people do. But you shouldn’t, and here’s why.
You can measure the efficiency of a dust cartridge filter by its differential pressure. This means measuring the pressure on the dirty air side of the filter and then on the clean air side. This tells you how much the airflow is slowing down across the filters.
If your differential pressure is higher than the recommendation for your system, it’s time for a change. The filter cleaning system is not able to clean your dust collector filters anymore. It’s time to replace the filters.
There are companies that offer to clean your industrial dust collector filters instead of changing them. Usually, they do this by blasting them with high-pressure compressed air to blow the accumulated dust out of the filters. The problem is that dust collector cartridge filters are made of cellulose and polyester, which means a large part of the filter is cardboard. When you try to clean industrial dust collector filters this way, the high-pressure air will create holes in the filter material.
You might not be able to see the holes. It may seem like the filter cleaning worked perfectly. The filters get put back in the dust collector, and the differential pressure is much lower.
The pressure isn’t lower because the filters are clean, though. It’s lower because air is going straight through the little holes torn in your filter.
How big a problem are those little holes in the cartridge filters?
Cleaning your dust collector filters can put holes in them, but how much dust is really going to get through those tiny holes? The answer is “a lot”. Air follows the path of least resistance. The filter material has resistance. The holes don’t. The air going through the dust collector cartridge filters will go through the holes, taking dust with it.
This is a serious problem for several reasons.
First, dust will be getting through your dust collector filters. Depending on where your air is venting, it’s going out into the environment or back into your facility. Either way, this could result in fines or health problems for employees.
Second, dust that gets through the filters can build up in the clean air plenum. There should never be dust in this part of the collector. The dust in there will keep blowing out into the facility even if you fix the filters.
Third, the differential pressure will be lowered because air can easily get through the holes. This could make it look like the filters are clean and working well, even though they are damaged. This makes it hard to recognize that the dust collector filters are not doing their job.
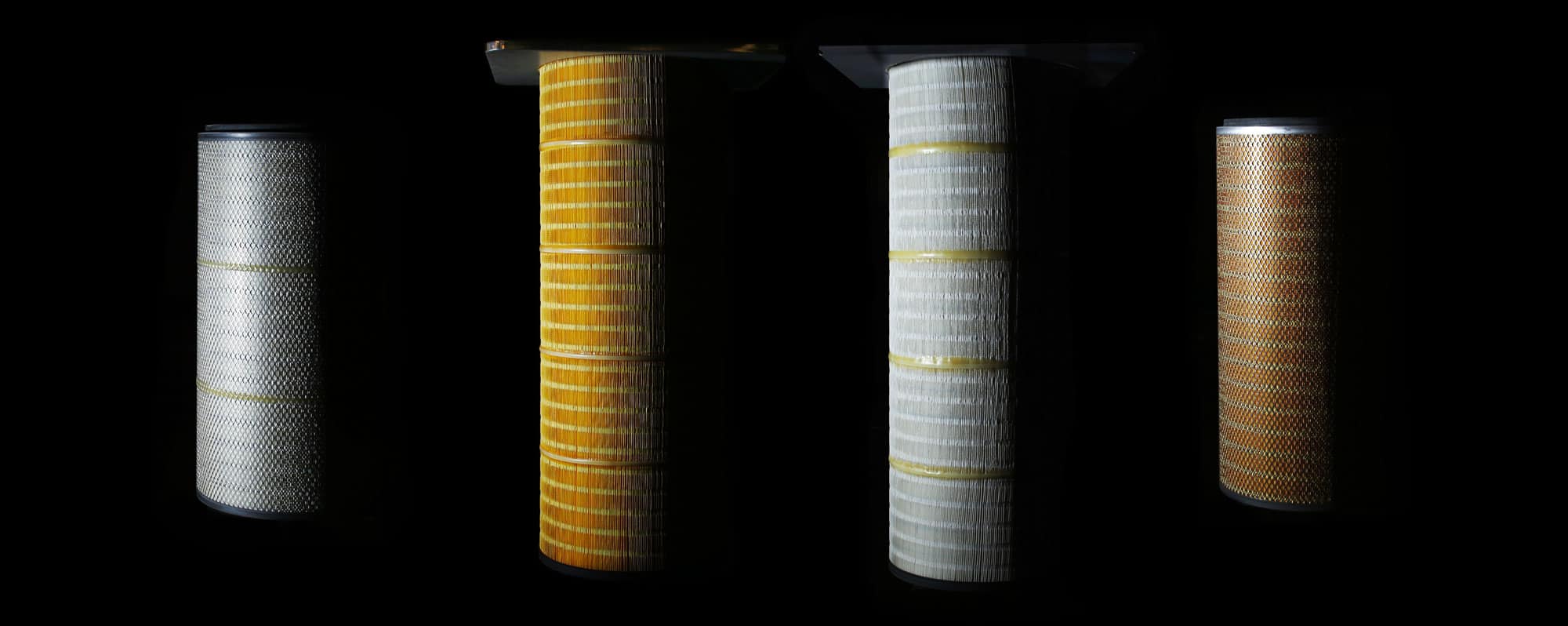
You’re Not Saving Money by Cleaning Your Dust Collector Cartridge Filters
Industrial dust collector filters are made of a cardboard-based material that is not made to be cleaned and re-used. While it looks like the filters are cleaned and working better, what you’re really seeing is filters that have been damaged. Learn more about filter cleaning versus installing new filters and offline cartridge filter cleaning.
Instead of trying to save money by having your filters cleaned, contact Imperial Systems and ask us about DeltaMAXX filters. They last longer than the competitors’ filters, so you’ll save money on your industrial dust collector filters over time.
Read more
by Erin Long | Jan 23, 2019 | Weld Fume
This weld fume extraction guide takes a look at the many ways to collect and remove weld fume from a facility. When not properly taken out of the work area, weld fume can cause some serious health issues for welders.
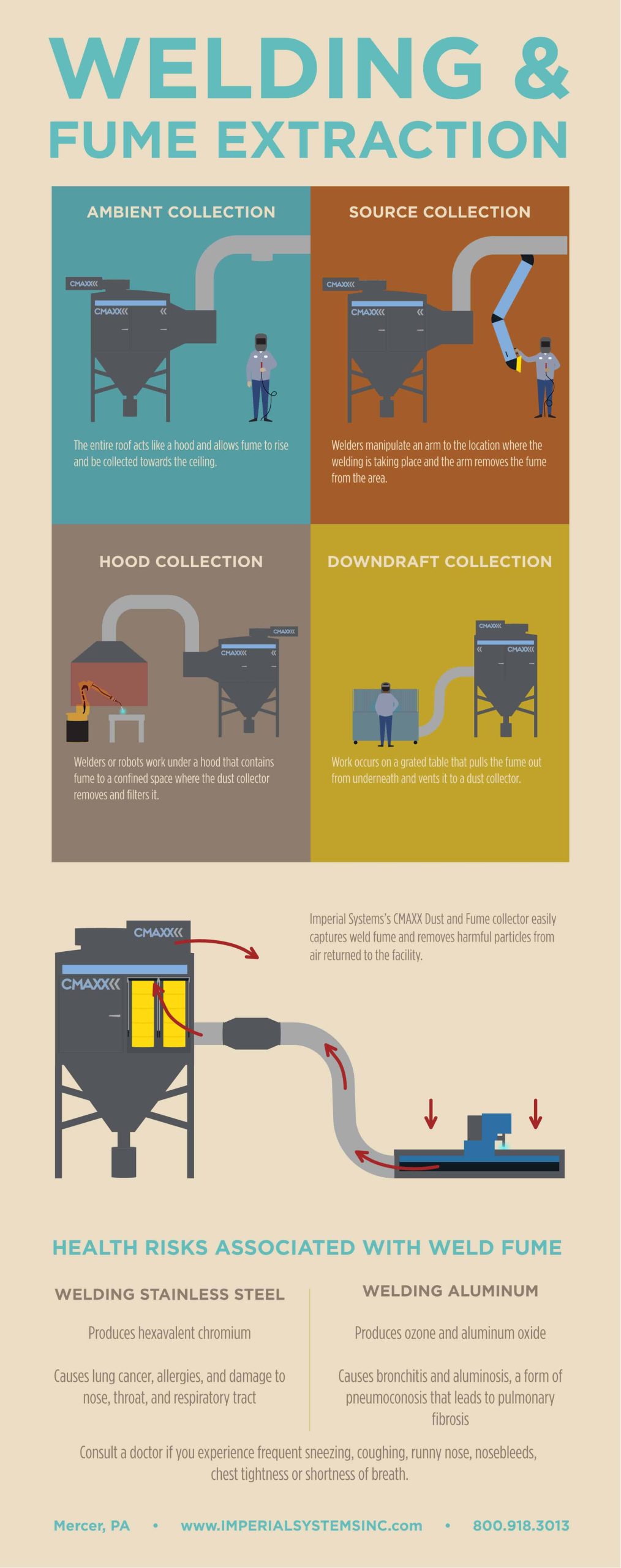
Weld Fume Extraction Methods
- Ambient Collection – The entire roof acts like a hood and allows fume to rise and be collected towards the ceiling. Ductwork runs with inlets above the work area to clear the fumes.
- Source Collection – Welders manipulate an arm to the location where the welding is taking place and the arm removes the fume from the area.
- Hood Collection – Welders or robots work under a hood that contains fume to a confined space where the dust collector removes and filters it.
- Downdraft Collection – Work occurs on a grated table that pulls the fume out from underneath and vents it to a dust collector.
Health Risks Associated with Weld Fume
Welding Stainless steel
- Produces hexavalent chromium, a dangerous valence state of the element chromium. Chromium metal is added to alloy steel to increase hardenability and corrosion resistance.
- Causes lung cancer, allergies, and damage to the nose, throat, and respiratory tract
Welding Aluminum
- Produces ozone and aluminum oxide. TIG, MIG, and plasma-arc welding typically produce ozone, a highly toxic gas. Aluminum oxide forms from the base and filler materials and exists in the welding fumes.
- Causes bronchitis and aluminosis (aluminum lung), a form of pneumoconiosis that leads to pulmonary fibrosis
Consult a doctor if you experience frequent sneezing, coughing, runny nose, nosebleeds, chest tightness, or shortness of breath.
Weld Fume Extraction Equipment and Experts
The CMAXX Dust & Fume Collector by Imperial Systems is the best choice for removing weld fume from your facility and keeping your employees safe. Our sales and product engineers will design and dust and weld fume collector specifically for your application. Contact us today.
Read more