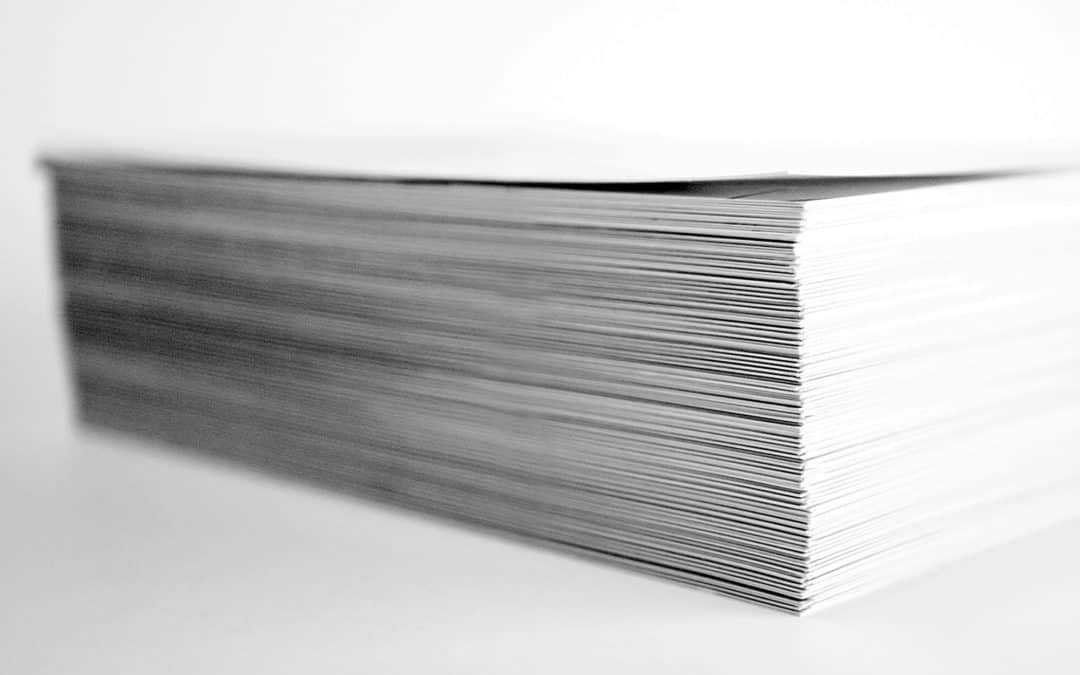
Case Study: Paper Recycling Mill Dust Causes Health and Safety Issues
Problem: Dust from Non-stop Production
An international supplier of commercial printing paper and newsprint had a serious dust issue. That is to say, this paper recycling mill in West Virginia dealt with extremely heavy dust from their non-stop production schedule. It runs 24 hours each day, 365 days every year. Specifically, the belt conveyors constantly produced airborne dust. As a result, it accumulated up to seven inches deep around some of the machines.
NFPA standards for wood and paper production specify safety measures, and this facility struggled to meet them. Other than dust masks, employees had little protection from the clouds of dust. One plant manager noted, “we were capturing 400-500 pounds of dust weekly. It was a huge problem.”
Besides irritating the eyes and lungs of employees, the large amount of dust created a huge fire hazard. Due to the fact that wood dust ignites easily, its airborne state can lead to a series of deadly explosions throughout a facility. Because of the concern for the health and safety of employees, the company began seeking solutions to become safe and NFPA compliant.
Solution:
The paper recycling mill searched for a company to assist them with dust control. Among the suppliers, they chose Imperial Systems, Inc. “Imperial is a one-stop-shop and we really value that when bidding out the job,” explained a plant managed. “Imperial took care of the entire process from the drawings to the engineering, to the fabrication, and clear through installation. The communication between us and them was always thorough.”
The company purchased a reverse-air BRF baghouse. Then Imperial Systems designed and installed the entire system, including ductwork. The design of the system met all NFPA standards. The new system immediately began to reduce airborne dust. Subsequently, dust stopped accumulating around the facility.
As a result, employees reported fewer problems with inhaled dust and with dust irritating their eyes. In addition, the fire risk greatly decreased with the removal of the combustible wood dust. Further, without dust piling up and obstructing the machines, the company saw improved production and fewer issues with the equipment.
Feedback: Paper Recycling Mill is Now NFPA Compliant
The plant manager said that the entire team from Imperial Systems was knowledgeable and efficient, as well as respectful, helpful, and easy to work with. The company is pleased with the experience of working with Imperial Systems.
“The install crew was a pleasure to work with. The whole process was a pleasure, actually. Imperial was very easy to work with. There was no lack of communication. I know if I need something in the future, I can call in and somebody from Imperial will be here as soon as possible.”
The paper recycling mill is now NFPA compliant. They have minimal wood dust in the facility and the fire hazard is greatly reduced. The company reports that the dust collector continues to run without issues, and they continue to be satisfied with their choice.
Read more