by Greg | Jun 21, 2013 | Case Studies
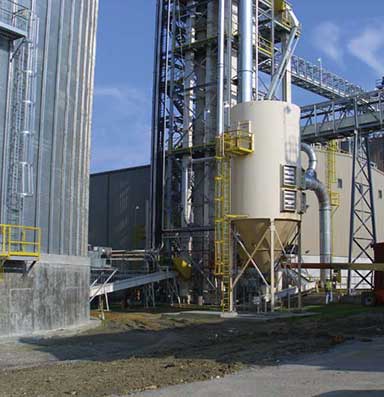
The First Commercial Scale Barley to Ethanol Plant Chooses Imperial Systems Turnkey Dust Collection System
Product: Turnkey Dust Collection System
Application: BioFuels
Customer: Barley-to-Ethanol Plant
Challenge
The contractor specified a turnkey dust collection system for the customers’ brand new barley-to-ethanol, state-of-the-art facility in the United States. Their products include: Barley Bio Ethanol, Barley Protein Meals and Barley Fuel Pellets. The challenge was finding a turnkey dust collection company to handle all of their dust collection needs.
Solution
The contractor is a long-standing customer of Imperial Systems, Inc. The contractor contacted Jeremiah Wann, President, for a bid on the project.
Jeremiah Wann designed a turnkey system which included: a BRF with an 8:1 ATC (Receiving Line), a Pulse Jet with a 7:1 ATC (Storage Line), another Pulse Jet with a 7.9:1 ATC (Load Out Line), a 1,900 CFM Standard Efficiency Cyclone, a 3,000 CFM Standard Efficiency Cyclone and all of the duct and fittings.
The customer wanted a turnkey system and Imperial Systems, Inc. was the only bidder able to provide the design, manufacture the equipment and install the system.
The customer is very pleased with the job and especially with Imperial Systems, Inc. ability to engineer, manufacture, and install.
Read more
by Greg | Jun 19, 2013 | Case Studies
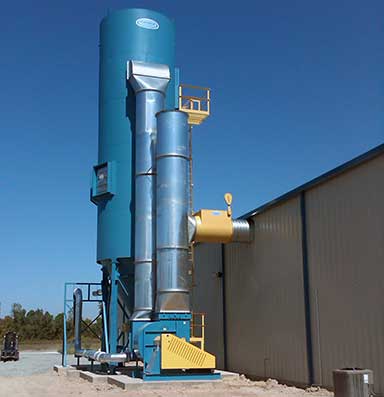
Top Moulding Manufacturer Selects an Imperial Systems Baghouse Dust Collector.
Product: Turnkey Dust Collection System
Size: 33,000 CFM Imperial BRF Reverse Air Baghouse Model 10BRF255-12
Application: Mixed Woods
Customer: Top Wood Moulding Manufacturer
Challenge
A top manufacturer of wood mouldings built a new facility and was in need of a dust collection system to handle the sawdust “blow-back” from the equipment.
Solution
The wood moundings manufacturer visited Imperial Systems, Inc. booth at the International Woodworking Fair in Atlanta, GA.
Imperial Systems, Inc. engineered, manufactured and installed the entire dust collection system. The system contains a 10-255BRF12 Reverse Air Baghouse and all duct and fittings.
The main reason that the wood moulder chose to go with Imperial Systems, Inc. is because Imperial could provide a turnkey dust collection system.
“Just wanted to let you know how much we appreciate you working with us on this project and how pleased we are with the results. The installation crew did an excellent job and we are all amazed just looking at the system. The entire system is running great!”
For more information on wood dust extraction systems, contact us. We’ll put you in touch with one of our specialists.
Read more
by Greg | May 19, 2013 | Case Studies
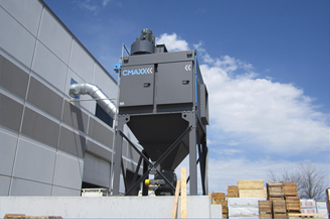
Product: CMAXX Dust and Fume Collector, Duct, Fittings and Install
Application: Welding and Cutting Fumes
Customer: Precision Tooling Manufacturer
Challenge
The Precision Tooling Manufacturer has a proven track record of manufacturing high quality, precision tooling. The manufacturers’ emphasis is on customer satisfaction, quality workmanship, quick turnarounds and employee safety.
The Precision Tooling Manufacturer decided to invest in a dust and fume extraction system to protect their employees from welding and cutting fumes and contacted Imperial Systems, Inc. through their website.
Solution
Imperial Systems, Inc. engineered, manufactured and installed the entire dust collection system. The system incorporates a CMAXX CM06 Dust and Fume Collector with DeltaMAXX filters, hoods for the welding stations and all duct and fittings.
The Precision Tooling Manufacturer chose to go with Imperial Systems, Inc. because of the vast knowledge of the engineering department and the high level of confidence in the sales team. The Precision Tooling Manufacturer said that the system is performing above all expectations and Imperial Systems achieved the goal of the project. The installation went very smooth. The field crew was fully dependable and always clean and neat.
After one-month of continuous operation, the DeltaMAXX filters are running less than 1” w.g.
“The installation went very smooth. The IMP field crew was fully dependable and always clean and neat. All around good-people.” – Plant manager, Precision Tooling Manufacturer
Read more